Is a filler metal (electrodes & welding rods) grouping for qualification, and is based essentially on their usability characteristics which determine the ability of welders to make satisfactory welds with a given filler metals. Prolonged temperatures in excess of 1500 f. Special alloys and tempers are often required to overcome this problem. Contact alcotec for assistance in alloy and temper selection when elevated temperature service is a concern. Alcotec wire corporation 2750 aero park dr., traverse city, mi u.s.a. 1-800-228-0750 fax 231-941-9154. The F number grouping of filler metals refers to their similarity on their usability characteristics. The usability determines the ability of a welder to deposit a sound weld metal with a certain filler metal. 625 filler metal is used in the Gas Tungsten-Arc (GTAW), Gas-Metal-Arc (GMAW) and Shielded-Metal-Arc (SMAW) welding Processes.
Over the years, several different temperatures have been used to define the concept of brazing. When the American Welding Society (AWS) published its first Brazing manual back in 1955, brazing was officially defined using 800F as the liquidus temperature of a brazing filler metal (BFM), above which temperature a joining process using that BFM would be defined as “brazing” (see Fig. 1). If the liquidus temperature of the filler metal was lower than 800°F, a joining process using such a filler metal would be called “soldering”.
First of all, then, let’s define what we mean by the “liquidus” temperature of a BFM. When any BFM is heated, it will reach a temperature at which it will start to melt. Below that temperature the BFM will remain solid, but once it crosses that temperature it will start to melt. That temperature is called the “solidus” temperature of the BFM. Then, as heating continues and more and more of the BFM melts, it will finally reach a point where all the BFM has finally melted, and become completely liquid. It will be said to have crossed the “liquidus temperature” for that BFM. Technically, the “liquidus” temperature is determined by, and defined as, the temperature at which a molten BFM begins to solidify upon cooling from its fully-molten state. But for our purposes here in this article, I will merely assume that when a BFM crosses its liquidus temperature during heating, it will become fully liquid (molten). Liquation is not being considered.
With this added information in hand, let’s go back to look at the early definition for brazing, back in the year 1955. At that time, AWS said that a joining process was considered to be “brazing” if a BFM had a liquidus above 800F, and the joining process was accomplished without melting any of the base-metal being joined, i.e., the joining process occurred “below the solidus temperature for the metals being joined”. That definition remained in effect for many years.
However, as the years have passed, and the world has “grown much smaller” because of electronic communication advances, and the development of high-speed aircraft transportation that can literally get us physically from one side of the globe to the opposite side in only a matter of hours, the old definition of brazing needed to be re-evaluated in order to take the metric world into consideration, since the majority of the world uses metric measurements, not British-based units.
This brings up another very important factor that needs to be understood, namely, what was the basis for choosing “800°F” as the defining temperature in the first place. Take a look at Fig. 2, which shows a “thermometer” scale with the melting temps for a variety of different pure metals.
Notice that near the bottom of the thermometer is a group of metals (zinc, lead, cadmium, tin, etc.), and that there is a significant temperature gap between zinc (787°F) and aluminum (near 1220°F). It was therefore felt to be convenient to pick a nice “even number” such as 800F (just above the melting temp of zinc), to officially define brazing.
Thus, 800F merely represented a number “pulled out of the air”, representing a convenient, even number somewhere between the melting point of zinc and aluminum, for the purpose of creating a written definition, and had no real metallurgical significance beyond that.

The metric world, however, found such a number to be inconvenient, and obviously would want to choose to define brazing a bit differently, while still placing their chosen temperature somewhere in that gap between the melting temps of zinc and aluminum.
But, in order to present a “unified” picture to the world, a compromise was needed in how to define the temperature that would be used to separate brazing and soldering. In subsequent meetings of the AWS Committee on Definitions, Symbols, and Metric Practice, it was, first of all, agreed that the primary system for measurement should be metric (SI), and then, that 450°C would be the temperature to be used in the definition of brazing, as shown in Fig. 3.
I am personally a bit surprised that because the line that separates soldering and brazing is a completely artificial line, merely picked “somewhere between the melting points of zinc and aluminum” for the convenience of a definition, why wasn’t 500C the final, agreed-to temperature selected instead of 450°C, just as the earlier AWS committee here in the US had chosen the nice, even number of 800°F?
Perhaps it was because the various committee-members deliberately sought to offer a compromise between the worlds of C and F, while, at the same time, not changing the approximate temperature of brazing too radically. Thus, the people involved settled on 450C, since that didn’t “significantly” change the degree-F numbers too greatly, and yet still moved the definition to a degrees-C number as the primary one.

Thus, when the brazing world officially adopted 450°C as it’s defining temperature, it thereby moved the degrees-F temperature for brazing from 800F up to about 840°F.
However, always remember that there is NO significance to the actual temperature number selected to separate the worlds of soldering and brazing.
When people ask me: “Why was 840°F selected for the definition of brazing? Is there some special metallurgical reaction occurring at that temperature?” — my answer is: “No, the 840°F is merely the approximate temperature conversion for 450°C, which itself is just a convenient, even-number pulled out of the air to officially separate brazing from soldering.”
IMPORTANT: A cautionary note to readers: Remember, the official temperature to use for defining brazing is 450°C, not 840°F. 840°F is merely an approximate conversion of 450°C (the actual conversion being 842°F), and is thus put in parentheses next to it, as 450°C (840°F). If you switch those two around and put the degrees-C in parentheses behind the 840°F, remember that the 840°F is the “approximate equivalent” temp, and the degrees-C is the primary! Some writers of brazing articles make the mistake of writing 840°F (449°C), as if the 840°F was primary, and was the exact temperature to use to define brazing. That is wrong! The 450°C is the official temperature defining brazing, and the 840°F is only an approximate equivalent, not the other way around.
What Is Filler Metal F Number
DAN KAY BRAZING SEMINARS: 3-Day seminars provide intensive training in “The Fundamentals of Brazing”, covering the brazing of materials ranging from aluminum to titanium to ceramics! FIND OUT MORE
Filler Metal F-no 6
Dan Kay – Tel: 860-651-5595: – Dan Kay operates his own brazing consulting/training company, and has been involved full-time in brazing for 40-years. Dan regularly consults in areas of vacuum and atmosphere brazing, as well as in torch (flame) and induction brazing. His brazing seminars, held a number of times each year help people learn how to apply the fundamentals of brazing to improve their productivity and lower their costs. Contact information for Dan Kay (e-mail, phone, fax, etc.), can be found by visiting his company’s website at: http://www.kaybrazing.com/To View a listing of all Dan’s articles please click here
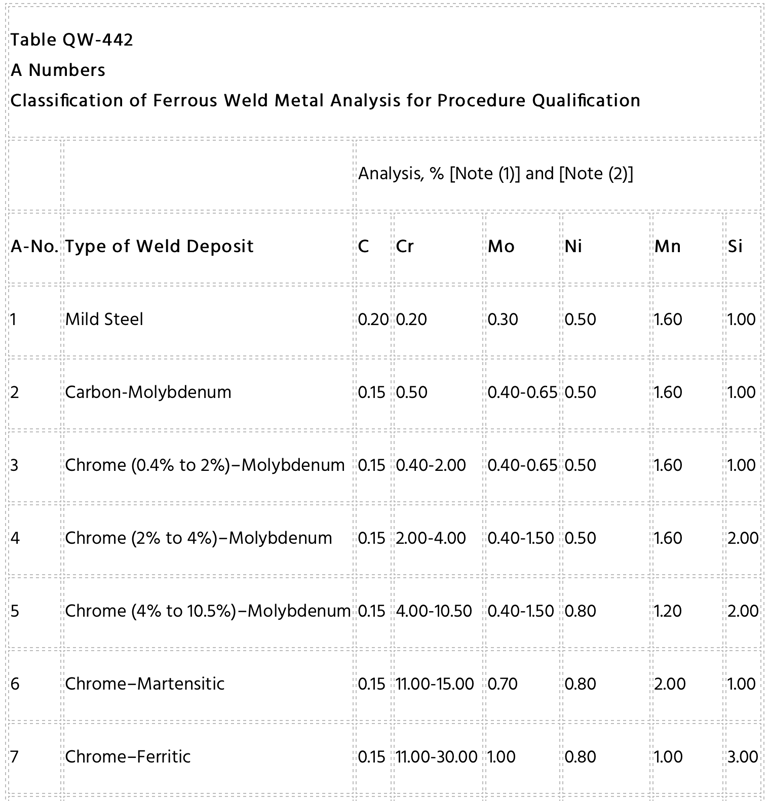
Read Dan Kay’s Biography
© Copyright Dan Kay 2014
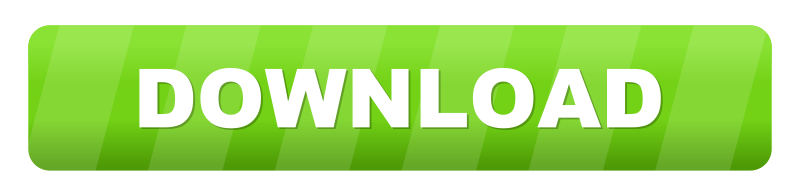
Comments are closed.